A research study was done in SAMK’s machine and production technology’s laboratory, in which the goal was to see if a welding seam could be done in realtime with a thermal imaging camera. Welding technologies that were used were; MIG-, TIG- and Synergiv MAG-welding. A thermal imaging camera used was FLIR ThermaCAM SC3000, which wavelenght is 8-9 µm. For image capturing and analysing, ThermaCam Researcher 2.8 PRO-program was used.
After the research study, the conclusion was that the welding seam or it’s parts cooling would be seen in the thermal image clearly. Also the hottest temperature could be seen and it’s location also the spreading of the heat could be seen in the metal clearly. Because every pixel’s temperature is known, the temperature distribution could be followed easily. Thus the automatic tracking of welding is obviously possible.
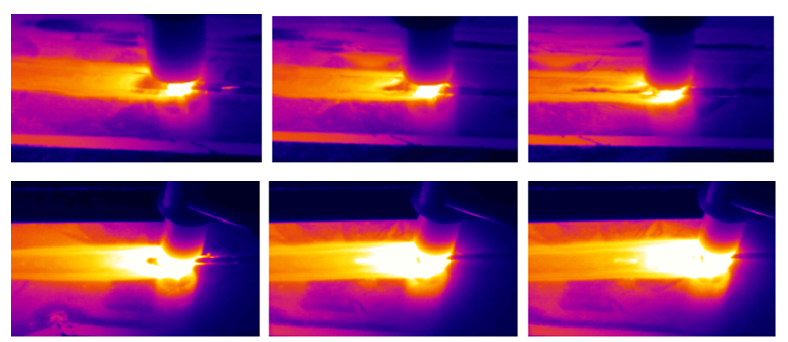
The challenge of the test imaging sessions were to create the errors into the welding seam that are easily recognized or known. Also in long welding seams, moving the thermal imaging equipment proved out to be a bit difficult task. Imaging sessions did give stable results on the fact that thermal imaging could be used in inspecting welding seams in real time. The research should be continued and bring the equipment to factory conditions to test how it would handle it.